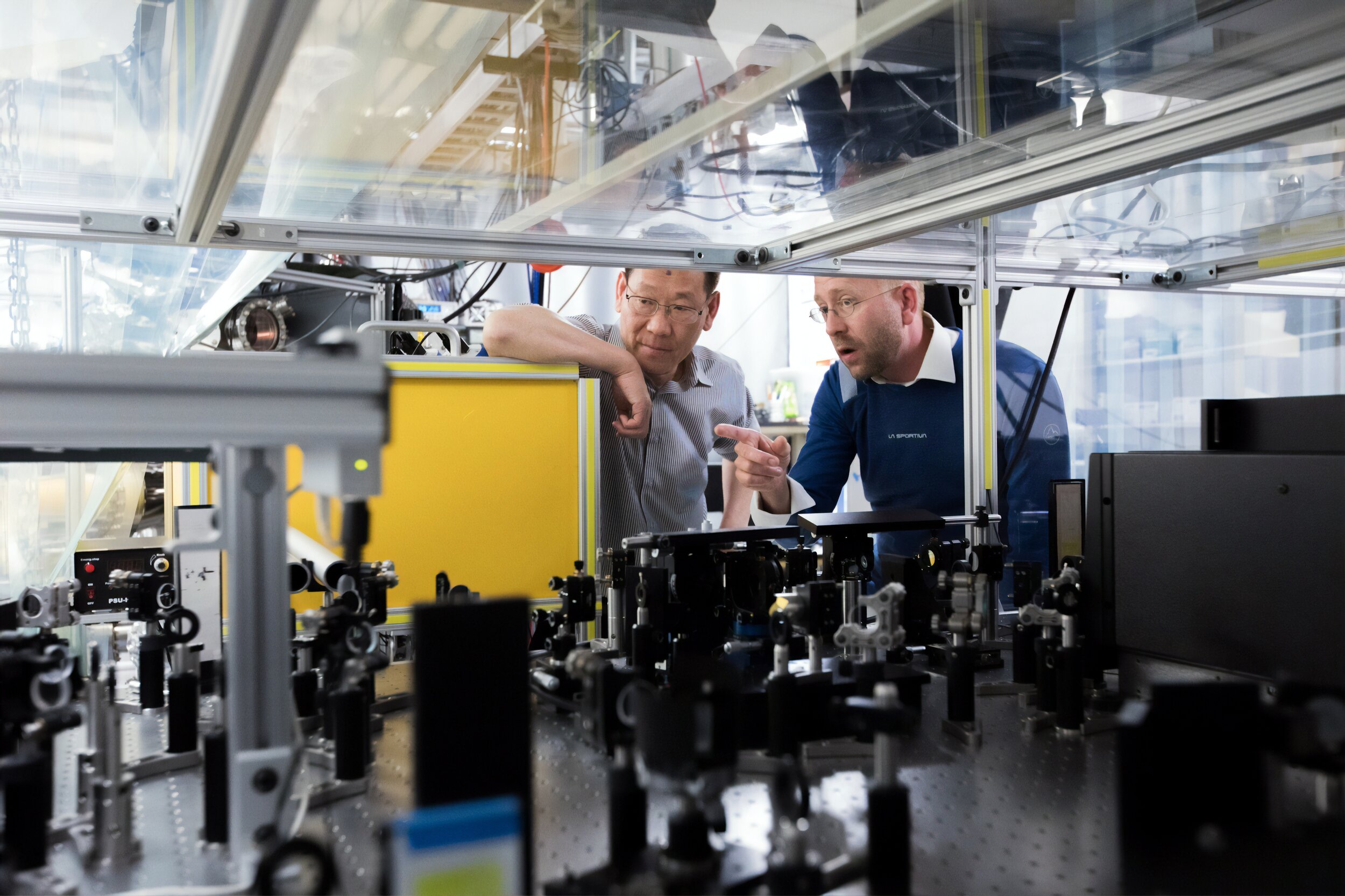
Sourcing Reports
Q. Does ordering a Sourcing Report mean you'll consult on our mass production process?
No it does not. The Sourcing Report revolves around finding, researching, and vetting high-quality manufacturers for your specific product. It does not cover advisory or consulting services in the mass production process.
Q. How do you check a supplier’s legal status?
We request and verify the business license of each supplier to ensure that the company is legally registered. In addition, we also make an assessment based on their registered capital and location. If needed we'll contact our network to verify the information.
Q. How do you verify documentation and manufacturing capability for each supplier?
A supplier's business license is verified directly with the Chinese city or province authorities, where the supplier is registered. Product certificates, test reports, and QMS certificates (if any) are verified through the issuing companies. We always attach scanned copies of these certificates in our reports for you to see. However, the manufacturing capability (e.g., MOQ, OEM, ODM, and Production Time) is based on information provided by the supplier. It, therefore, cannot be verified by a third party without a physical inspection.
Q. What if you fail to deliver the Sourcing Report?
If we fail to deliver the Sourcing Report because the product does not exist in any form, we will suggest a variety of similar products to do research on for you, or alternatively provide you with a refund.
Q. What is the delivery time for the Sourcing Report?
That depends on the complexity of your product. Our sales team will include an estimated timeline in the proposal for our services.
Q. We’ve already found one or more suppliers on our own, can you verify them?
Yes, we can do that, but we prefer to always find you at least a few suppliers on our own in order to be more informed on your product, and the spectrum of prices, lead times and quality of the product.
Q. Do you visit each supplier?
We visit each supplier that we work alongside in the mass production stage. Supplier visits are not included in the Sourcing Report but can be added on as an additional service if requested by the client.
Q. We have already found a few suppliers by ourselves. Can you include them too?
Yes, we can.
Q. What if I’m not satisfied with the result?
Whenever a customer expresses dissatisfaction, we always do our best to find a solution. This may be that we find additional suppliers, or allow the customer to select a new product. Our philosophy is to never leave a customer behind. That being said, we do not issue a refund after the process has begun, and the report has been delivered.
Project Management
Q. Why should I use your Project Management service or order a Sourcing Report from your company when I can find suppliers online, for free?
If you aim to manufacture a high-quality product smoothly, with assistance from Chinese sourcing professionals that will help you tackle all the issues you might face on the way, you should consider buying our services.
Q. Can I use your Project Management services, after I've already found a supplier or specifically for one or two stages of my project?
Yes, you can use our Project Management services after you’ve already found a supplier, but you can’t use it for a specific stage of manufacturing. If you are interested in hiring us for QC services, see below section.
Q. Will you negotiate the order on our behalf?
Yes, negotiation services are included in our Project Management service.
Q. Who are your Partners?
We partner with established Quality Control companies and Shipping/Freight Forwarders in Mainland China. We have been working closely with our partners for 5+ years and developed a robust and trusting relationship with each and every one of them.
Q. What kind of templates do you have?
Contracts, NDAs, Non-Circumvent Clauses, Non-compete, Inspections Templates, and Bill of Materials.
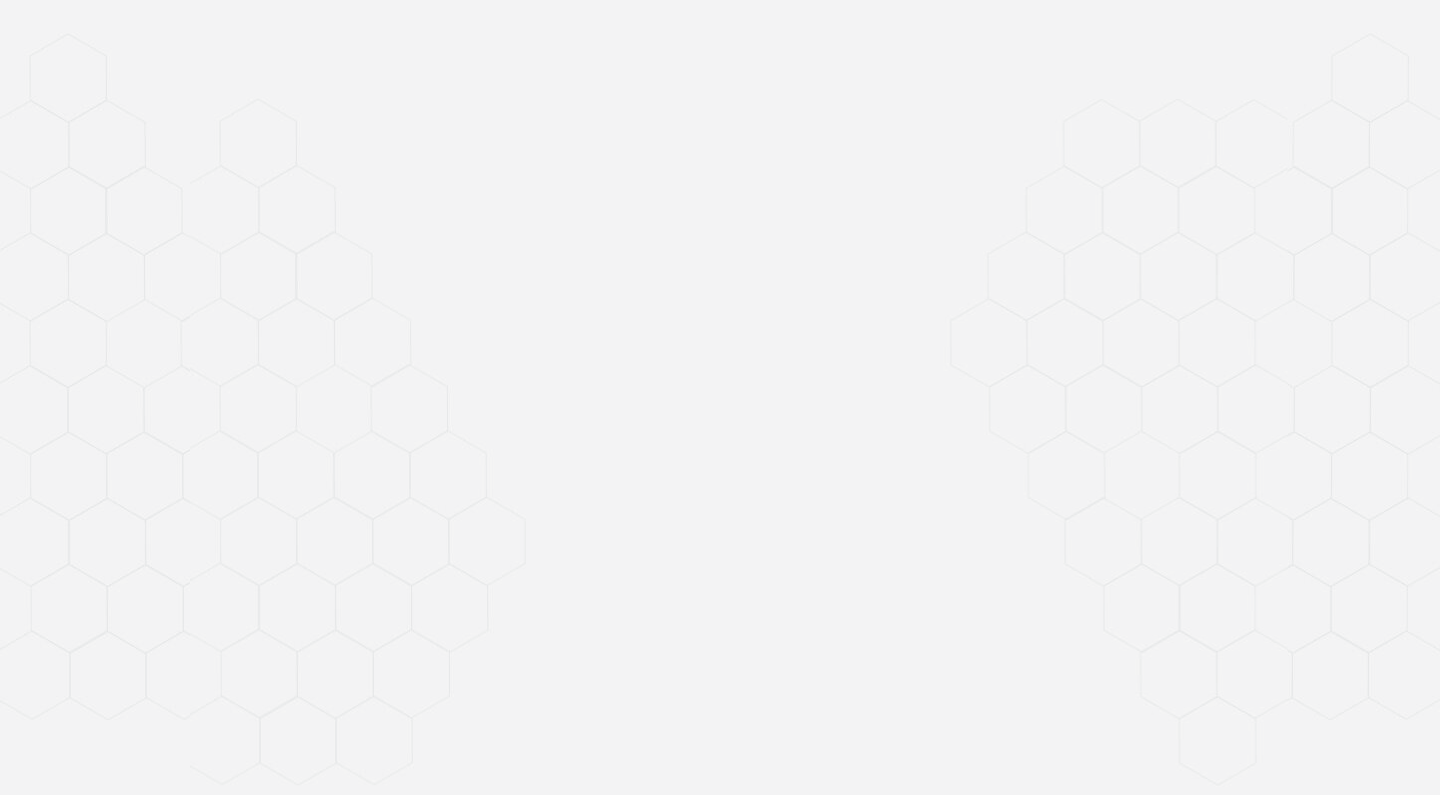
Quality Control
Q. On what factors do you select suppliers?
We select suppliers on a variety of different factors, but the five main factors are:
- Our relationship with the supplier
- The suppliers business history and past projects
- The communicational skills of the supplier
- The quality of the suppliers’ product
- The cost-effectiveness of the supplier compared to its peers
Q. What if I’m not satisfied with my final product?
It is very rare for us to go through our full production again because of the vetting process and inspections that we do. However, in rare situations, we will try our best to find the best solution for our customers. Example: Having the factory replace defective units, provide a credit/discount on the order, or re-manufacture the goods.
Q. What if I’m not satisfied with your Project Management Service?
Whenever a customer expresses dissatisfaction, we always do our best to find a solution. This may have an internal review with our Customer Success Manager, to find a more suitable workflow or even assigning a new Project Manager to you. The reason that our project management fee is monthly is because you are not entitled to a long-term contract. So when a customer is dissatisfied with our service, you’re not obligated to continue paying, as long as you provide us 15-day advance notice before your next payment is due.
Q. Will you guarantee that we avoid quality issues and compliance-related issues?
We do not offer any guarantees for this. We verify all the documents the factory provides us, assist you in setting quality standards for the product and perform quality control for you. However, we can not guarantee that the quality inspection will be a pass.
Q. What if your team does not have experience inspecting my product niche?
If we have no experience with some products, we work closely with trusted third-party QC partners to fulfill those requirements.
Payments
Q. Are there any additional expenses to project management?
Yes, there are usually additional expenses to project management. The most common costs include travel expenses to and from the factory, third party quality control expenses, local and international shipping expenses (if prototypes are being sent to us, and you).
Q. Do I pay the supplier, or do you?
For full transparency, our clients usually pay factory direct, but there are occasions where we’ll pay the factory on a customer’s behalf like when there’s an RMB payment required or if we have an alternative compensation structure with our customer.
Q. How do I pay the monthly consulting fee for a project?
You can pay us by Credit Card, Debit Card, or Wire Transfer. Consulting fees are paid on a monthly basis. You should pay our invoices upon receiving them; however, as our relationship grows, we can incorporate net payment terms.
Q. Can I pay via Credit Card?
Yes, we accept Credit Card Payments via Stripe payments. However, there is a 4% processing fee attached. We wouldn’t advise making payments via Credit Card over $1,400; a wire transfer would most likely be more cost-effective.
Q. If I need to pause my project, do I have to continue making monthly payments?
Yes, you can pause your monthly payments. But we need at least 15 days’ notice before payment is due.
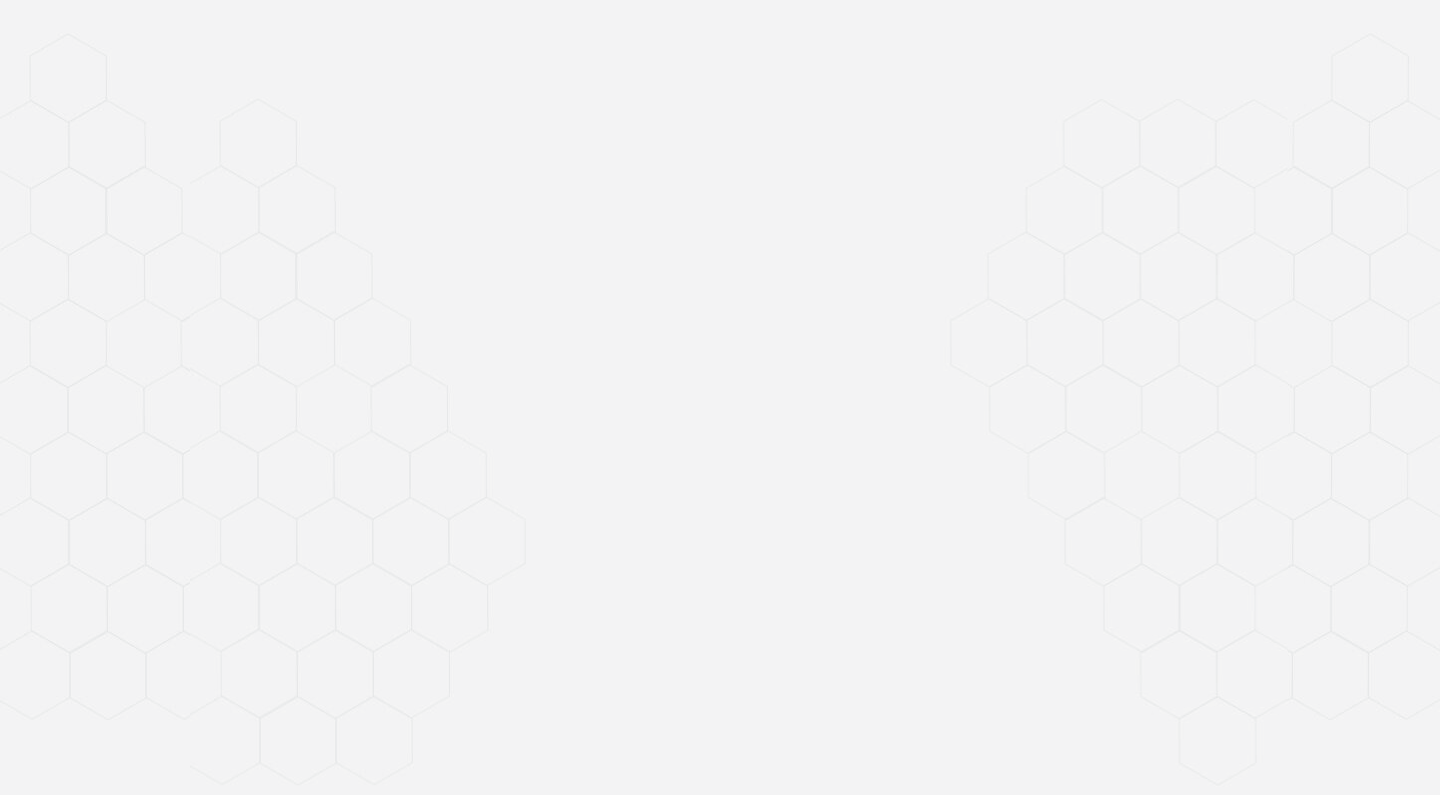
Technical Definitions
Q. What is OEM?
OEM stands for Original Equipment Manufacturer (a.k.a. White or Private Labelling). These are products that are typically manufactured by one company for sale under another company’s brand. These products typically have little or no modifications to them besides branding and packaging.
Q. What is ODM?
ODM stands for Original Design Manufacturer, these are typically products that are new designs and are brought to life in collaboration with a suitable factory. With the level of customization involved in the ODM production, it takes close attention to detail, in case there are possible design or manufacturing issues that have to be anticipated or resolved.
Q. What is a Quality Management System?
Also known as a Q.M.S. this where we try to verify that a factory has an actual system in place for them to prevent or reduce quality control issues. Every factory should have this, but unfortunately, that’s just not the case. We also provide tips to assist with how to start implementing your own Q.M.S.
Q. What is QC?
Q.C. stands for Quality Control, this is how to ensure you’re getting the best quality products possible to your customers. Typically through factory audits (inspections) prior to mass production and factory inspections during/or at the end of production. There are 3 main forms of inspections. The “Factory Audit” is conducted before mass production begins to inspect a factory’s capability to produce your precious goods. The “During Production Inspection” (a.k.a D.P.I. or Spot Check) to discover and fix any significant defects or mistakes early. The “Final Random Inspection” (a.k.a F.R.I.) usually performed after the production is completed, but prior to the goods leaving the factory and issuance of the final deposit - it is also the most common form of inspection.
Have more questions?
GET A FREE 15-MIN CONSULTATION TODAY
